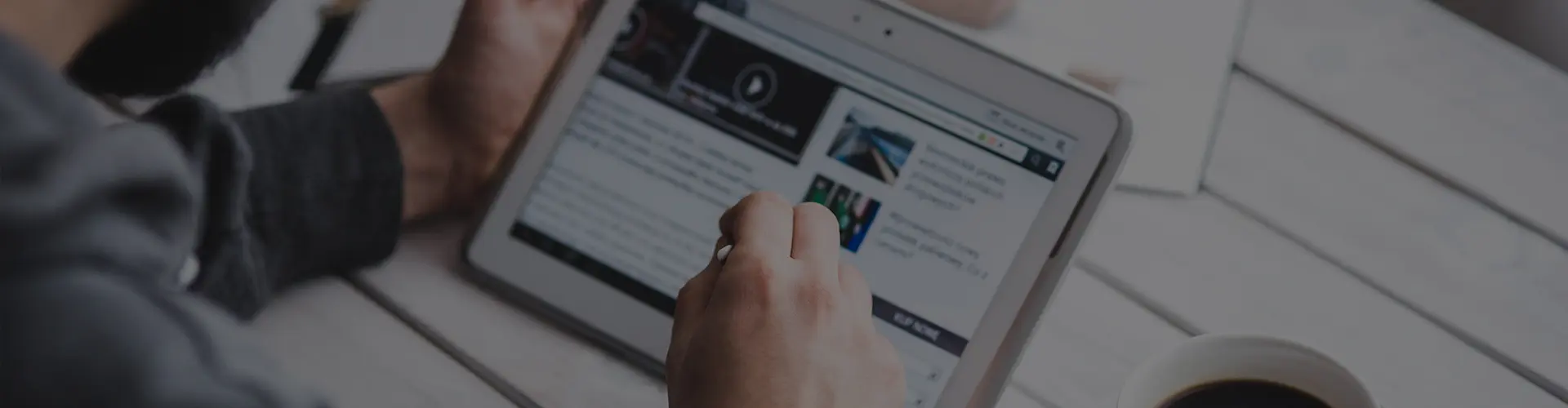
News
How to Choose the Best Prefabricated House for Your Global Sourcing Needs
In recent years, the demand for prefabricated houses has surged globally, as more consumers and businesses recognize their significant advantages over traditional construction methods. According to the Global Prefabricated Building Market report, the industry is expected to reach approximately $210 billion by 2027, growing at a compound annual growth rate (CAGR) of around 6.5% from 2020 to 2027. This growth is fueled by the increasing emphasis on sustainable building practices, cost-effective solutions, and the rising need for rapid construction options. As a result, stakeholders looking to source prefabricated houses must navigate a wide range of choices to meet their specific needs effectively.
Choosing the best prefabricated house requires a nuanced understanding of various factors, including materials, design flexibility, and compliance with local regulations. Moreover, a report by Research and Markets indicates that the adoption of prefabricated houses is particularly prominent in regions facing housing shortages and environmental challenges. As companies and individuals venture into global sourcing, equipping themselves with comprehensive knowledge about the prefabricated housing industry can lead to informed decisions that maximize both quality and value. This blog aims to provide insights and guidance on selecting the most suitable prefabricated house to fulfill diverse sourcing needs in an ever-evolving marketplace.

Understanding the Global Prefabricated Housing Market and Its Growth Potential
The global prefabricated housing market is witnessing significant growth due to an increase in demand for sustainable and efficient building solutions. As the world continues to recover from economic disruptions caused by the pandemic and geopolitical tensions, the prefabricated housing sector is positioned to thrive. Projections indicate that the market could reach a value of $36 billion by 2024, with an impressive compound annual growth rate of approximately 5.81% leading up to 2033. This growth is fueled by advancements in construction technology and a rising emphasis on environmentally friendly building practices. Countries like Vietnam are emerging as vital players in this market, as their real estate sectors rebound and present numerous acquisition opportunities. The ongoing restructuring in the Vietnamese real estate market is attracting foreign investment, amplifying confidence in the potential for growth within prefabricated housing. Furthermore, the global trend towards urbanization and the need for affordable housing solutions are driving the demand for prefabricated structures across various regions, enhancing the sector's viability on a global scale. As the landscape of global sourcing for prefabricated homes evolves, potential investors must carefully evaluate market dynamics, regional strengths, and technological advancements. Understanding the overall growth potential within the prefabricated housing market enables stakeholders to make informed decisions that align with their sourcing needs, ultimately paving the way for sustainable investments in this thriving industry.
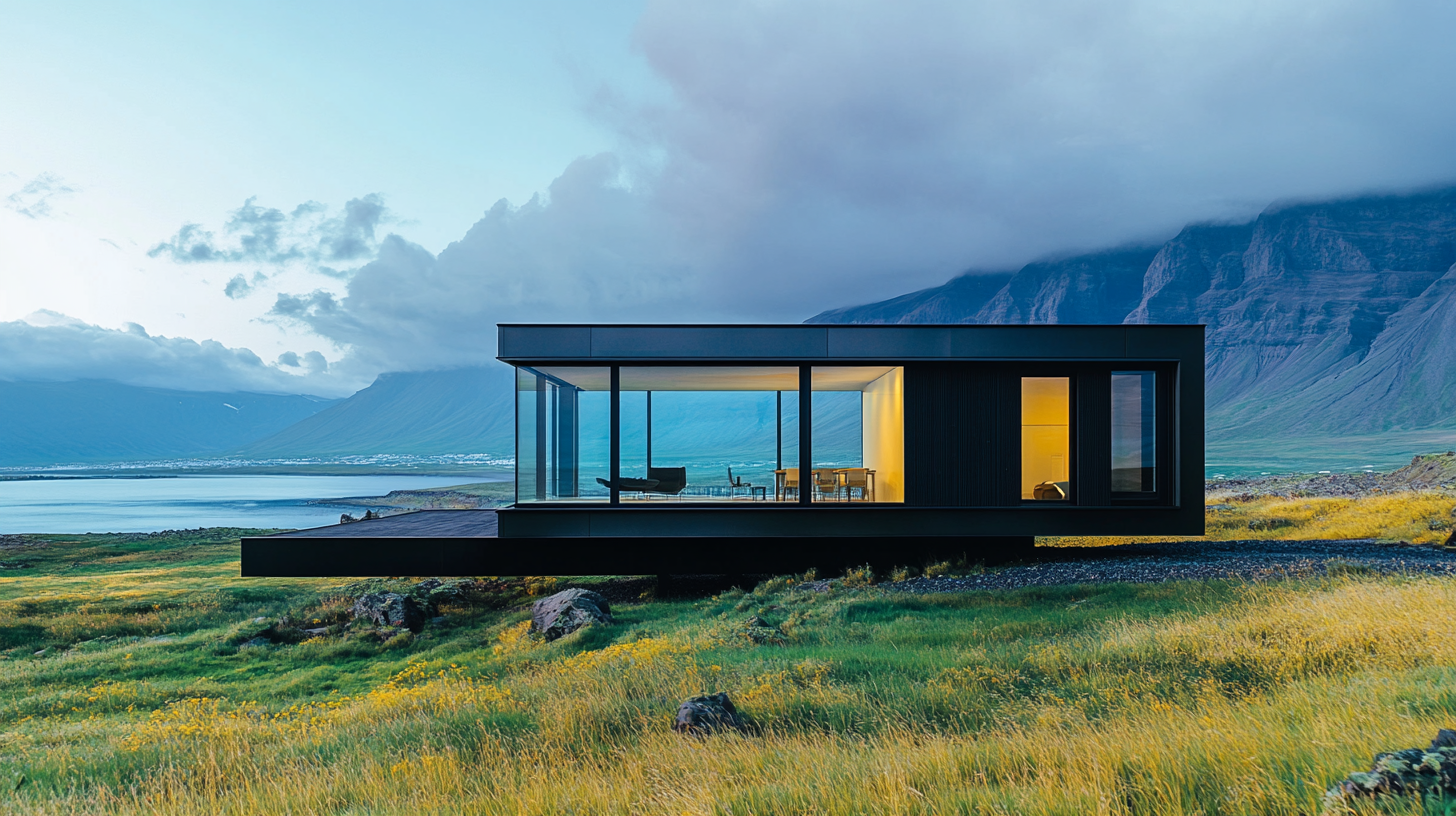
Key Factors to Consider When Selecting a Prefabricated House for Diverse Needs
When selecting the best prefabricated house for your global sourcing needs, several key factors must be taken into consideration. First and foremost is the cost impact throughout the entire process, which includes design, production, transportation, and assembly. Understanding these cost drivers is crucial, as they can significantly influence the overall budget and feasibility of the project. For instance, integrating strategies that focus on design for manufacture and assembly can help streamline the construction process and reduce expenses.
Another vital factor is energy efficiency and sustainability. Recent studies have shown that prefabricated buildings can be designed to optimize energy use and minimize environmental impacts. Incorporating features such as proper daylighting and energy-efficient materials can not only lower operational costs but also contribute to a greener future. As the demand for affordable housing rises, prefabricated solutions that emphasize these aspects can provide viable options that meet diverse customer needs.
Moreover, evaluating the scalability and modularity of prefabricated housing is essential. The potential to increase affordable housing stock through modular construction highlights an ongoing trend in the industry. This approach not only addresses housing shortages but also enables flexibility in design, accommodating various lifestyle preferences. By weighing these critical factors, you can ensure that your selection aligns with both current market trends and future demands.
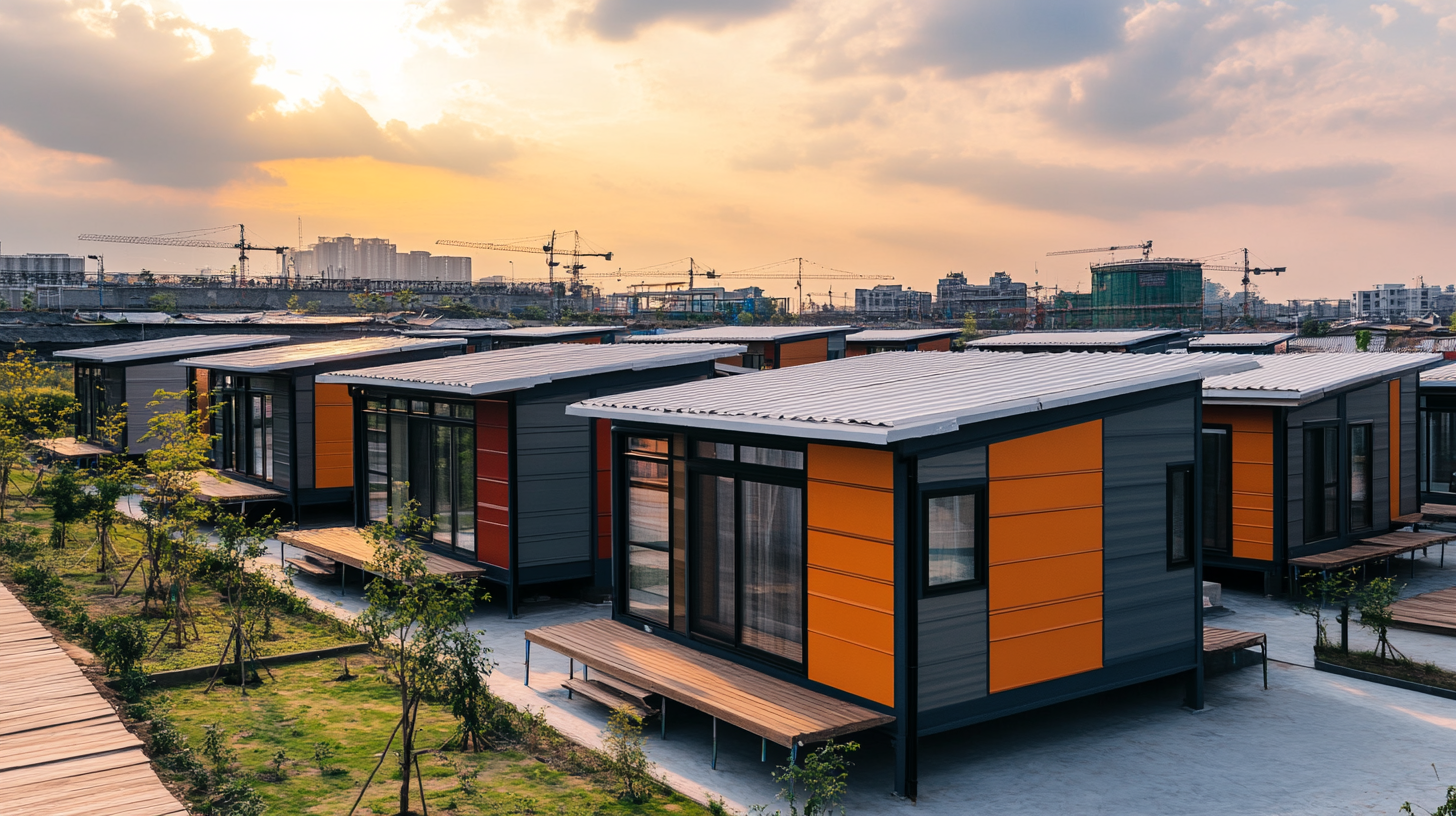
Evaluating Construction Methods and Material Quality in Prefabricated Housing
When selecting the best prefabricated house for your global sourcing needs, evaluating construction methods and material quality is crucial. Prefabricated homes are constructed off-site and brought to the desired location, which can significantly save time and labor costs. However, the quality of these homes hinges on the techniques employed during manufacturing. Researching the different construction methods—such as modular, panelized, and pre-cut—can help you determine which option aligns best with your quality standards and budget.
Material quality is equally important in ensuring the longevity and durability of a prefabricated house. Different manufacturers may offer varying grades of materials that impact not only the aesthetics but also the structural integrity of the home. For instance, opting for high-grade insulated panels can enhance energy efficiency, thus reducing long-term operational costs. It's essential to request samples and certifications for materials used, ensuring that they meet both local building codes and sustainability benchmarks.
In addition to these factors, consider the manufacturer's reputation and track record. Researching client testimonials and inspecting completed projects can give you insight into their reliability and craftsmanship. By prioritizing both construction methods and material quality, you can make an informed decision that satisfies your global sourcing needs while ensuring a durable and cost-effective living solution.
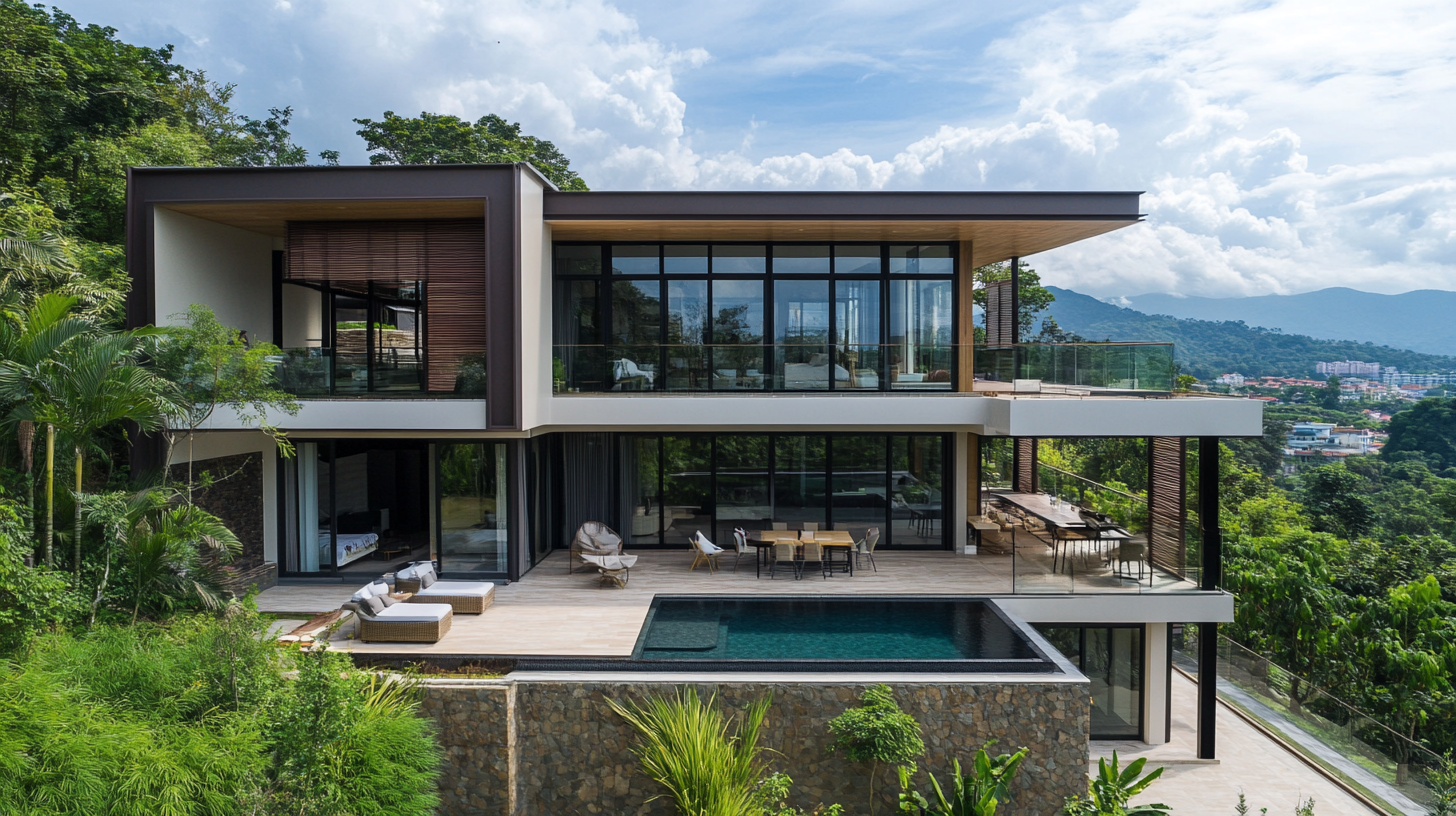
Cost-Benefit Analysis: Comparing Prefabricated Houses to Traditional Construction
When considering construction options, a cost-benefit analysis is essential for comparing prefabricated houses to traditional building methods. A 2021 report by McKinsey & Company indicated that prefabrication can reduce construction time by 20-50%, translating into significant labor cost savings over the project's duration. With reduced on-site construction time, resources can be allocated more efficiently, allowing builders to focus on other projects and maximizing their profitability.
In terms of investment, the initial costs associated with prefabricated houses can be surprisingly competitive. According to a study by Deloitte, prefabricated homes can cost up to 10-20% less than traditional builds, primarily due to lower labor costs and more efficient use of materials. Additionally, the controlled environment of a factory setting minimizes waste, which can further enhance cost savings. Furthermore, the speed of assembly means that return on investment is realized sooner, making prefabricated options attractive for developers looking to capitalize quickly.
Maintenance and energy efficiency also play vital roles in the long-term cost benefits of prefabricated homes. A recent report by the National Association of Home Builders (NAHB) found that homes constructed off-site often feature superior insulation and design innovations that can lead to reduced energy bills—by as much as 30% over traditional homes. This aspect not only provides financial savings but also aligns with growing consumer demand for sustainable living practices. Therefore, when weighing the cost-benefit implications, prefabricated houses emerge as a compelling option for modern construction needs.
Sustainability and Energy Efficiency in Prefabricated Housing: A Growing Priority
As the world increasingly prioritizes environmental sustainability, prefabricated housing is emerging as a frontrunner in meeting these global needs. Prefabricated homes are built in controlled factory environments, allowing for better resource management and reduced waste. This method not only streamlines the construction process but also significantly minimizes the carbon footprint associated with traditional building practices.
Energy efficiency is another critical factor in the growing preference for prefabricated houses. Many manufacturers are integrating advanced technologies, such as solar panels, high-performance insulation, and energy-efficient windows, into their designs. This innovation helps homeowners reduce their energy consumption and utility bills, while also contributing to a smaller environmental impact. By choosing a prefabricated house that emphasizes sustainability, buyers can benefit from lower operational costs and a greater sense of responsibility towards the planet.
Moreover, the shift towards sustainability in prefabricated housing isn't just a trend; it's becoming a necessity as climate change continues to pose significant challenges. As more people seek to align their living environments with eco-friendly values, the demand for prefabricated homes that prioritize energy efficiency will only increase. This evolution signifies a critical step towards a future where our living spaces complement our environmental commitments, thereby reshaping the landscape of global housing solutions.